In the demanding environments of oil and gas production and exploration, mud pumps play a crucial role in the efficient handling of abrasive mixtures. Central to the performance and longevity of these pumps is the fluid end, a component that directly impacts pump efficiency, maintenance frequency, and overall operational reliability.
Innovations in Fluid End Design
Recent advancements in fluid end design are setting new standards in mud pump performance. Manufacturers are leveraging state-of-the-art materials and engineering techniques to create fluid ends that withstand the abrasive and high-pressure conditions inherent in oil and gas operations.
Innovations such as the integration of ceramic liners and the use of corrosion-resistant alloys are significant. These materials not only enhance wear resistance but also contribute to a reduction in pump-related downtime, ensuring continuous and efficient operations.
Maintenance strategies for optimized performance
The maintenance of fluid ends is pivotal in maximizing pump efficiency and minimizing operational interruptions.
Regular inspection and timely replacement of worn components can prevent catastrophic failures. Operators should establish a routine maintenance schedule, focusing on the inspection of seals, valves, and liners within the fluid end assembly.
Employing condition monitoring tools can aid in the early detection of wear or damage, allowing for proactive maintenance and parts replacement.
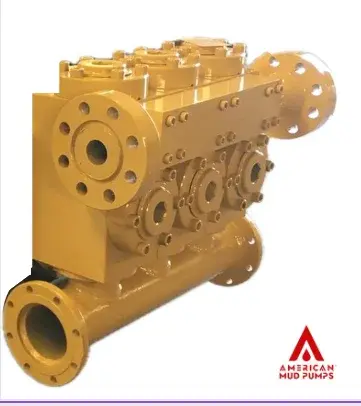
Addressing high-pressure and abrasive challenges
High-pressure and abrasive mud environments pose unique challenges to fluid ends. To address these, the industry is moving towards fluid ends designed with robustness in mind.
High-grade materials that offer superior strength and wear resistance are becoming the norm. Additionally, fluid end designs now often include features that facilitate easier maintenance and quick part replacement, minimizing downtime.
Recommendations for industry professionals
Embrace innovation: Stay informed about the latest materials and technologies in fluid end design. Consider retrofitting existing pumps with advanced fluid ends to enhance performance and durability.
Prioritize maintenance: Implement a comprehensive maintenance program that includes regular checks and early wear detection. Utilize condition monitoring systems to predict and prevent failures.
Material selection: Choose fluid ends made from materials suited to your specific operational conditions. The right material can drastically reduce wear and extend the life of the pump.
Partner with experts: Work with manufacturers and specialists who understand the challenges of your particular environment. Their expertise can guide you in selecting the right fluid end components and maintenance practices.
By adopting these advanced fluid ends and adhering to best practices in maintenance, oil and gas professionals can significantly improve the efficiency, reliability, and longevity of their slurry pumps. This not only ensures smoother operations but also contributes to the overall success and profitability of their projects.
Comments