What is the purpose of the crosshead in the mud pump?
- American Mud Pumps
- Aug 23, 2023
- 2 min read
Crossheads play a crucial role in mud pumps. At American Mud Pumps, we are committed to serving our customers by offering spare parts and services. But what exactly do we mean when we refer to crossheads?
Importance of the Crosshead in a Mud Pump:
Transmission of Motion: The primary function of the crosshead is to transfer and convert the rotary motion of the crankshaft into a reciprocating linear motion. This motion is used to drive the piston of the mud pump.
Protection: The crosshead ensures that the rotary motion from the crankshaft and the associated lubricants do not contaminate the linear system of the piston and the drilling fluid. This is crucial, as contamination could cause damage to the piston, the mud pump, and even the well being drilled.
Guidance: It provides guidance and alignment to the piston rod, ensuring straight and smooth movement. This is essential for the efficient functioning of the mud pump and for minimizing wear and tear.
Absorption of Side Loads: The crosshead absorbs any side loads or off-axis forces that might arise, ensuring that the piston moves straight and true. This is vital for the efficient operation of the mud pump and for extending the life of the pump components.
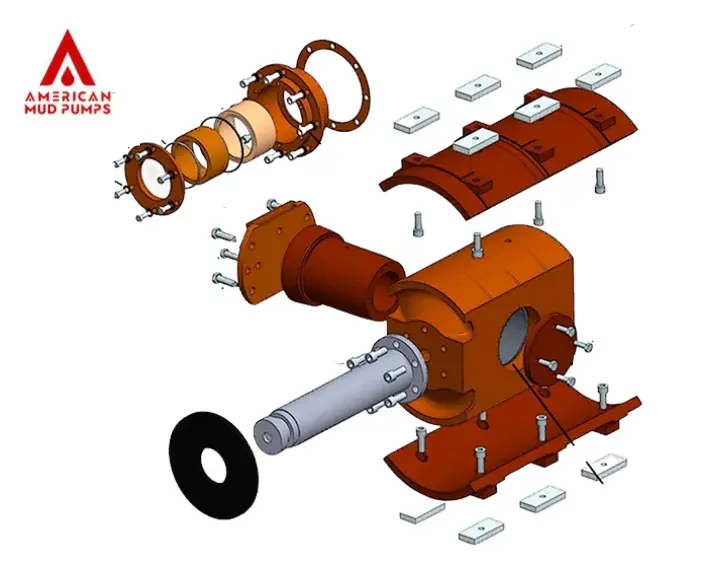
Parts that Make Up the Crosshead:
Crosshead Body: This is the main component that provides the sliding mechanism to convert rotary to linear motion.
Crosshead Pin: This pin connects the crosshead to the connecting rod, enabling the transmission of motion.
Crosshead Guides: These are guides, often made of metal plates, that ensure the straight-line movement of the crosshead.
Crosshead Slipper: It's an additional guiding component that might be present in some designs to stabilize the crosshead's movement.
Lubrication System: Most crossheads come with their lubrication channels or mechanisms to ensure minimal wear and tear due to friction.
Characteristics of the Crosshead:
Robust Design: Given the high pressures and forces involved in mud pumping, crossheads are designed to be sturdy and to handle these extreme conditions.
Tight Tolerances: Precision is crucial in drilling operations. Thus, crossheads are manufactured with tight tolerances to ensure efficient operation and minimize unwanted sideways movement.
Wear-resistant: Since they are continuously in motion during drilling operations, crossheads are typically made of wear-resistant materials or are designed with replaceable wear surfaces.
Lubrication: Effective lubrication mechanisms are integrated to minimize friction, reduce wear, and extend the lifespan of the crosshead and associated components.
Ease of Maintenance: Many modern crossheads are designed for easy maintenance and replacement, ensuring minimal downtime for the drilling rig.
Commentaires